WPC wallboard, full name Wood Plastic Composite Wall Panel, is a wood-plastic composite wallboard, which is a new type of building material made of wood powder, plastic and other additives. It combines the advantages of wood and plastic, and has the characteristics of high strength, weather resistance, corrosion resistance and easy processing, and has gradually become a popular choice in the field of indoor and outdoor decoration and construction. The following will briefly introduce the development process of WPC wall panels.

The concept of WPC wall panels first appeared in the 1990s, when wood-plastic composites were recognized as a new type of material. The early WPC wall panels were mainly made of wood powder and polyethylene through extrusion molding process. They have the natural beauty of wood and the characteristics of easy cleaning and maintenance of plastic, and are gradually used in indoor and outdoor wall decoration. However, the early WPC wallboards had some problems, such as poor weather resistance, color change, etc., which limited their development in practical applications.
With the continuous development of technology, WPC wall panels have experienced several milestone breakthroughs. The first is the improvement of raw material technology. Traditional WPC wallboards use wood powder as the main raw material, but wood powder has deep grooves and high water absorption, which can easily lead to problems such as expansion, deformation and mildew of the board. In order to improve these problems, the new raw material technology began to adopt a better wood powder treatment method to reduce the grooves and water absorption in the wood powder, and added some preservatives and anti-ultraviolet agents to improve weather resistance and anti-aging performance.

The second is the improvement of process technology. With the advancement of extrusion molding technology, the production process of WPC wallboard has also been improved. The traditional extrusion molding process is replaced by a more advanced and efficient co-extrusion technology, which achieves better appearance and structural strength by extruding two plastics of different colors and materials at the same time. At the same time, the molding technology is added to make the texture of the WPC wallboard more rich and real, improving its decoration and aesthetics.
The process technology improvement of WPC wallboard refers to improving the quality, performance and production efficiency of WPC wallboard by improving the production process and optimizing the production process. The following are some common WPC wall panel process technology improvement measures:
Material formula optimization: By changing the formula ratio of WPC wallboard, such as adjusting the ratio of wood powder and plastic, the amount of additives, etc., to obtain better performance and appearance. For example, increasing wood fiber content can improve the strength and weather resistance of siding, while reducing plastic content can help improve environmental performance.

New extrusion molding technology: Traditional extrusion molding technology mainly uses a single-layer extrusion die, but such wallboards are prone to problems such as surface unevenness, air bubbles, and color difference. Modern extrusion molding technology adopts co-extrusion technology, that is, extruding two plastics of different colors and materials at the same time, so that the wallboard has better color uniformity and surface texture.
Molding technology: Molding technology is to directly press the surface texture and pattern of WPC wallboard through the mold, so that the wallboard has a more real and natural texture effect. This technique can make the wall panel look more beautiful and increase its decoration.
Thermal compression technology: thermal compression technology is to process the WPC wallboard under high temperature and high pressure, so that the density of the wallboard is increased and the bonding force is stronger. This increases the strength and durability of the siding and reduces problems such as warping, cracking and water absorption.
Surface coating technology: In order to increase the weather resistance and anti-fouling properties of WPC wallboard, surface coating technology can be used for treatment. This technology can add a layer of protective film to the surface of the wallboard, which plays the role of durability, waterproof and anti-pollution.

Improvement of mechanical equipment: With the advancement of technology, the mechanical equipment for producing WPC wall panels is also constantly improving. For example, modern extruders can better control temperature, pressure and extrusion speed, improving product quality and production efficiency.
In addition, the concept of green environmental protection and sustainable development has played a positive role in promoting the development of WPC wall panels. With people’s attention to environmental protection and sustainable development, the production process of WPC wall panels begins to pay attention to the rational use of resources and the recycling of waste. A large number of recycled plastics and waste wood are used as raw materials, which reduces the dependence on natural resources and reduces waste emissions, which meets the requirements of sustainable development.
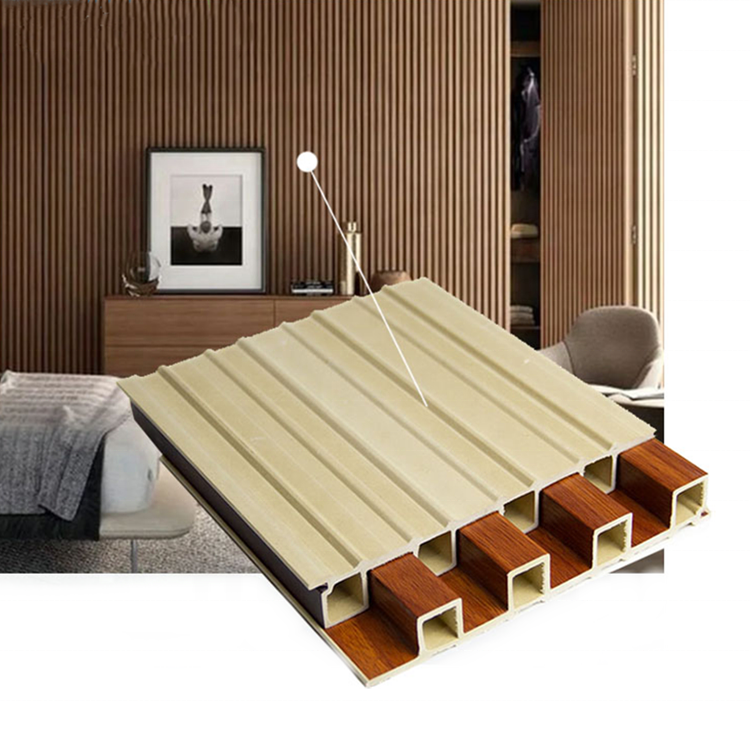
To sum up, after years of development and technological improvement, WPC wallboard has been significantly improved from the initial raw material composition to the current process technology and environmental protection performance. In the future, as people’s demand for environmentally friendly materials continues to increase, WPC wall panels will continue to strive to improve the quality, durability and sustainability of materials, and become one of the main choices in the field of architecture and interior decoration.